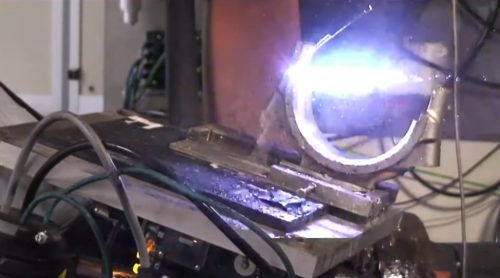
Laser peening imparts beneficial stresses to extend the useful life of metal components.
Materials experts at LSP Technologies design laser peening surface treatments for each part, using variables like the power energy of the laser, length of the laser pulse, and the angle of attack. The result is a precision laser peening treatment that extends the useful life of components.
Once our material scientists have analyzed your metal component, we optimize the laser peening process to meet your requirements for reliability, endurance, and safety. We use finite element analysis and our deep library of experience with metal parts to save time in prescribing laser peening parameters accurately and efficiently.
Throughout this discussion of Laser Peening Parameters, or variables of the process, we refer to adjustment capabilities of the Procudo® Laser Peening System, the first commercially available laser peening system for sale or lease.
In addition to the Procudo® System, LSP Technologies also offers custom laser peening solutions for manufacturing facilities, as well as laser peening services and application development.
Laser peening produces measurable compressive residual stresses typically 1-2 mm deep below the metal surface. In some cases laser peening penetrates up to 12 mm below the surface. These deep compressive residual stresses counteract tensile stress on parts operating at high speed or subject to other forces that lead to corrosion and cracking.
Power Density
The power density equation’s variables contain key parameters for precision laser peening.
The energy level, spot size, and pulse width of the laser determine the Power Density in Laser Peening, which is expressed as an equation in which Power Density is Gigawatts per square centimeter. Power Density can also be expressed as Energy divided by the product of the pulse width (in nanoseconds) times the laser spot area in square centimeters.
Depth
Deeper stresses mean more protection for mission-critical metal components.
The deeper these stresses penetrate through laser peening, the better we can improve fatigue life and fatigue strength for metal parts.
Laser peening can typically create these beneficial stress patterns 1-2 mm deep from the surface, 10 times deeper than conventional treatments. Shot peening typically provides only 0.2 mm of residual stress.
Higher power density produces deeper compressive residual stress. Wider spot sizes spread out the power, increasing the speed of the processing but diminishing the depth of compressive stresses. In isolation, we can see that the force of the shock wave has mechanically distorted and expanded metal grain shapes. The grid they occupy looks wider and flatter.
Energy
Light amplifiers control the energy of laser pulses delivered to the part.
Although the laser beam wavelength of the Procudo® Laser Peening System remains constant, the phase of light amplifiers determines the energy level of the beam, up to 10 joules of power in the 200-watt Procudo® System.
See the video below from Cutting Edge Optronics on laser light amplifiers.
Pulse Width
Measuring the length of the laser beam pulse.
The pulse width is the length of time the beam emits light, measured in nanoseconds. The Procudo® Laser Peening System uses pulses lasting 8-16 nanoseconds to produce the plasma shock wave that imparts compressive residual stress.
Spot Size
Smaller spot sizes produce more concentrated laser peening power at the surface of the part.
The laser beam impact area at the surface of the part is the spot size. With a constant level of energy and pulse width, a smaller spot size creates higher power density (GW/cm2). A larger spot size diffuses the same amount of energy over a larger surface, diluting surface power density but increasing the processing rate.
Angle
Complex shapes benefit from laser peening’s consistency over a wide range of angles.
Aiming the laser beam from a wider angle increases the spot size, which lowers the power density. Regardless of the beam angle, however, laser peening creates a shock wave that is perpendicular to the surface of the part.
This holds true, even if the part has a convex or concave shape. Complex shapes, curves, and hard to reach areas of parts can benefit from this predictable effect.
Frequency, or Pulse Rate
Pulse rates up to 20 Hz mean faster coverage for components.
The pulse rate is the frequency at which we are emitting laser shocks to apply sudden pressure to the metal surface. The Procudo® Laser Peening System can achieve up to 20 Hz, or 20 shocks per second, helping it cover larger surface areas quickly.
Spot Pattern
Dense and overlapping patterns of laser peening enhance compressive stress.
The robotic controls of the Procudo® Laser Peening System can create a pattern of spots on the part for optimum fatigue life extension, controlling the overlap of new areas of compressive residual stress.
We can set up the number of spots, as well as patterns of spot coverage, to increase the magnitude and depth of compressive residual stresses produced by laser peening. Repeated laser peening in the same regions of the part has the effect of deepening beneficial compressive residual stress.
Procudo® Laser Peening System Product Data Summary
Laser peening imparts beneficial stresses to extend the useful life of metal components.
Precision applications for components through modeling and a deep library of metal surface data.
Leading, innovating, and serving major customers since 1995.
Want to find out more?
We begin by understanding your parts, their purpose, and operating conditions.
Then we use computer modeling, as well as our extensive library of industry applications to show how laser peening can meet your needs.
Let us show you how laser peening can extend the operating life of your part by 3-10 times.