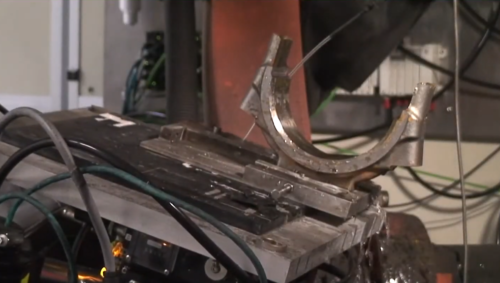
We spray a consistent layer of water over the part, forming a transparent overlay.
Deterrence Against Metal Fatigue
Laser shock waves penetrate deep into metal surfaces. creating residual stress patterns to counteract corrosion, cracking and other symptoms of metal fatigue.
Here’s how we deliver protection to extend the life of mission-critical metal components by 10x or more.
Look under the surface of metal to see how laser peening penetrates deep into metal surfaces, counteracting corrosion, cracking, and other symptoms of metal fatigue.
Laser peening protects mission-critical components from metal fatigue 10 to 15 times longer than competing processes, fighting many symptoms of metal fatigue.
And since laser peening is a mechanical surface enhancement process, not a heat treatment, it preserves metal shapes and properties.
A tightly controlled pulse of high-energy laser energy generates shock waves that propagate through the target material and produce compressive residual stresses.
Our brochure tells the story of Laser Peening — the process, the benefits, how it prevents metal fatigue, and an introduction to Laser Peening Equipment
We spray a consistent layer of water over the part, forming a transparent overlay.
The energy of the laser beam sets off an expanding plasma at the surface of the metal. Water contains the resulting shock wave into the surface of the part.
Repeated laser peening in a proven pattern provides consistent protection of a part's targeted areas.
This step-by-step approach shows how the laser peening process
applies pressure to metallic structures, represented as the blocks of a grid.
Step 1
The high energy laser beam hits the metal surface.
The red shading and arrows represent
the laser pulse arriving at the metal surface.
Step 2
A plasma shock wave applies pressure
to the metal, reshaping its microstructure.
In isolation, we can see that the force of the shock wave has mechanically distorted and
expanded metal grain shapes. The grid they occupy looks wider and flatter.
Step 3
Distorted metal pushes up against
surrounding metal structures.
If we look at the plastically deformed section as it continues to live on in the overall grid,
we can see that its larger shape pushes up against the parts of the metal not affected by laser peening.
Step 4
Surrounding metallic structures adapt to the expanding metal.
The surrounding metal elastically adapts to the enlarged volume
of the metal affected by laser peening.
Step 5
Healthy compressive residual stresses form.
The arrows show how compressive residual stress affects metal after laser peening.
The laser peened region in red has become larger, pushing outward.
The surrounding metal regions are trying to push inward to get back to their original shape.
The sum of these two opposing forces comprise compressive residual stress,
which helps prevent surface corrosion and cracking.
The Result
Deep compressive stresses extend
the useful life of components.
Laser peening produces measurable compressive residual stresses typically 1-2 mm deep below the metal surface.
In some cases laser peening penetrates up to 12 mm below the surface.
These deep compressive residual stresses counteract tensile stress
on parts operating at high speed or subject to other forces that lead to corrosion and cracking.
For an in-depth look into the precision and flexibility of laser peening for individual parts, learn more about Laser Peening Parameters.
Want to find out more?
We begin by understanding your parts, their purpose, and operating conditions.
Then we use computer modeling, as well as our extensive library of industry applications to show how laser peening can meet your needs.
Let us show you how laser peening can extend the operating life of your part by 3-10 times.